Back to MEAM.Design - Laser Cutting - Notes on Press Fits
First, you should ALWAYS MEASURE YOUR STOCK - you'll find that even though we call it 1/8" or 1/4", it tends to vary.
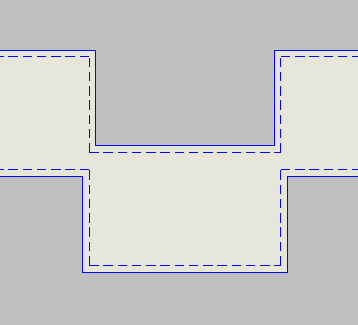
The Enemy: Laser Kerf
The laser itself has a diameter, which results in a certain amount of material being removed when cutting. Because the laser will cut away material centered along the geometry that you define, the theoretical total width of material removed is the radius of the laser, or the kerf. This is nominally 0.007", although it varies with material type and thickness. Generally, a thicker material results in a larger kerf—this is because the higher power and slower speeds results in more material being removed at cut. To generate decent fits between mating parts, you must take this kerf into account when designing them. The effect of this kerf can be visualized in the image to the right, where the dashed line represents the cut line, and the solid bodies are what would be left after cutting. If you were to try to assemble these together, there would be a significant amount of wiggle room (approx. 0.014 inches - enough for 3 or 4 sheets of paper).
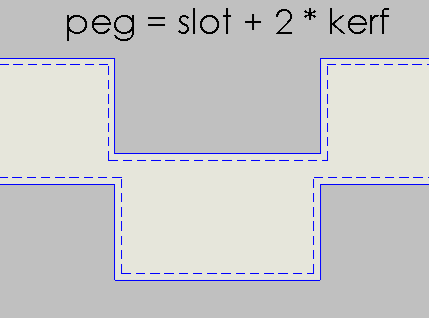
Getting a Line-on-Line Fit
In order to generate a line-on-line fit between the parts (as shown in the image to the right), you could either enlarge the tab, shrink the slot, or do both. For the purposes of this example, the width of the tab is set to be equal to the width of the slot plus twice the kerf (0.014").
Getting a Decent Press-Fit
With somewhere between 0.001 and 0.002 inches of dimensional overlap, you should be able to create a quality press fit between two parts, though this is highly dependent upon a number of factors, including the compliance of the members and the magnitude of the dimensions. In other words, we could express this as
tab = slot + 2 * kerf + 2 * overlap
For more compliant (softer) materials, you'll want to increase the overlap. For instance, when trying to achieve a solid press-fit box joint with acrylic (which is relatively stiff), you may find 0.001"-0.002" of overlap to work well, while with MDF, you may find an overlap of 0.002"-0.004" to be suitable.
It can be a good idea to do a quick test cut to see what the kerf actually is in the material you are using. Kerf and cutting performance are also quite dependent upon both the laser focus and the cleanliness of the lens, so it's hard to give exact values for the overlap without doing some preliminary testing.